Beyond’s MPD software communicates directly with the Rig’s EDR system to get live data for pumps, standpipe, and pipe movement to accurately control the pressure.
Beyond’s control console can be accessed remotely by personnel in the office, which allows to support field personnel in troubleshooting and updates.
What is a control system?
The control system in MPD takes the inputs from various sensors like pumps, flow meters, pressure transducers and more. It uses the information with different algorithms and machining learning in its CPU to actuate the choke valves that control the pressures. These components work together to continuously monitor and adjust the pressure in the wellbore in real time and recommend how to increase performance.
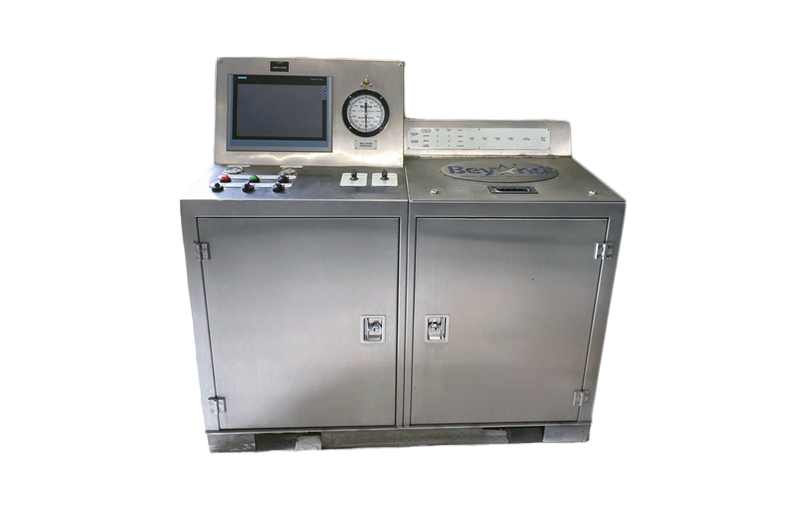
Hydraulic control system
Beyond’s original control system whereby the chokes are operated via pressurized hydraulic fluid in order to achieve accurate bottomhole pressure targets.
The current iteration is CSA C1D2 and C1D1 certified in different product forms.
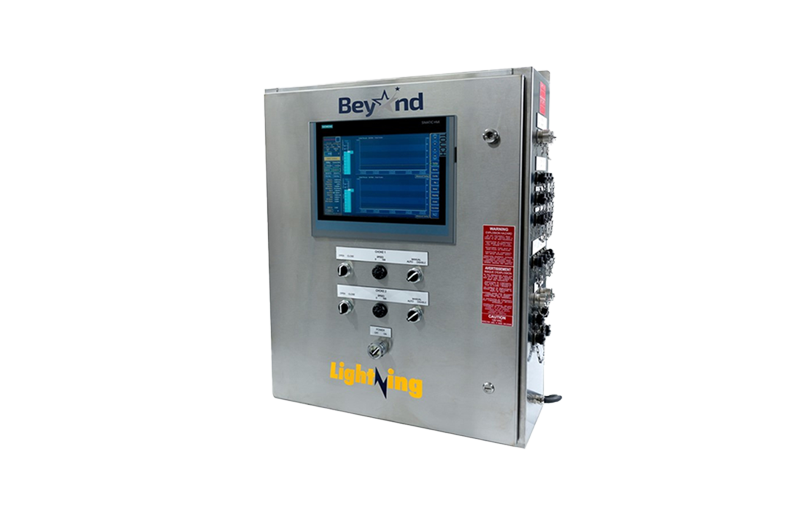
Electric control system
Beyond’s iteration in choke control where they are operated via electric current. This system includes all the features of the Hydraulic System, but in a smaller package.
The current iteration is CSA C1D2 certified. The next iteration will experience the system in a CSA C1D1 package.
The main objectives of the control system in MPD are:
-
Maintaining precise control over the downhole pressure is crucial in preventing wellbore instability, kicks, and other drilling-related challenges. The control system adjusts parameters to manage the pressure within the desired range.
-
The system constantly monitors downhole conditions using sensors and instruments. This information is then used to make real-time adjustments to drilling parameters, ensuring that the wellbore remains stable and within safe pressure limits.
-
The system is equipped with features to detect kicks (unwanted influx of formation fluids into the wellbore). Immediate corrective actions can then take place, such as adjusting choke settings or stopping drilling operations to reevaluate downhole conditions.
-
MPD control systems are designed to operate in an automated or semi-automated mode, allowing for quickly response to changes in flow without extensive manual intervention.
-
System logic that takes in rigs variables to provide a system target pressure to maintain target ECDs. This no longer needs constant input as the user can initiate and full tripping schedule that changes pressure based on speed and depth of the pipe being tripped and used in conjunction with Beyond’s proprietary Minerva Hydraulics™ (previously known as Real-Time Hydraulics).
-
MPD as a standalone product provides incredible benefits to the success of a drilling campaign. When integrated into a rig’s data system, Beyond can provide further benefits be improving communication speed between systems while being able to receive more system data to improve reporting and analytics. Some custom User Screens can created to assist the Driller’s Software Ecosystem.
-
This is the real-time engine application of Minerva. Multiple observation points can be observed and tracked in real-time while also providing the Pressure Targets for drilling ahead if desired. Future releases will see a tripping and roll-over engine be created.